Rapid Injection Molding: Revolutionizing Product Development Across Industries
In today's fast-paced manufacturing landscape, rapid injection molding is emerging as a game changer for product development across diverse industries. This innovative technique streamlines the process of creating molds and producing parts, enabling companies to significantly reduce lead times and costs. As businesses strive to keep up with consumer demands and market trends, rapid injection molding provides a versatile solution that enhances productivity and efficiency, making it an essential tool for modern manufacturing.
From automotive to healthcare, the applications of rapid injection molding are vast and impactful. It allows for the quick prototyping of components, ensuring that designs can be tested and refined with unprecedented speed. This not only accelerates the overall product development cycle but also fosters greater collaboration between engineering teams and stakeholders. As industries look to innovate faster and deliver high-quality products, the role of rapid injection molding becomes increasingly vital in maintaining competitiveness and meeting customer expectations.
Benefits of Rapid Injection Molding
Rapid injection molding offers significant time savings in product development. Traditionally, injection molding involves lengthy lead times for tool fabrication and testing. With rapid injection molding, the process is streamlined, allowing for quicker iterations of prototypes and final products. This expedited timeline helps companies respond faster to market demands and reduces the time to launch new products.
Another key advantage is the cost efficiency associated with rapid injection molding. This method typically requires lower upfront investment compared to conventional tooling, making it an attractive option for startups and smaller businesses. By using faster and more flexible manufacturing techniques, companies can optimize material usage and reduce waste, leading to lower overall production costs.
Lastly, rapid injection molding enhances design flexibility. Engineers and designers can experiment with complex geometries and optimize designs without the constraints often found in traditional molding. This freedom allows for innovation, enabling the development of products that better meet consumer needs and stand out in competitive markets.
Applications in Various Industries
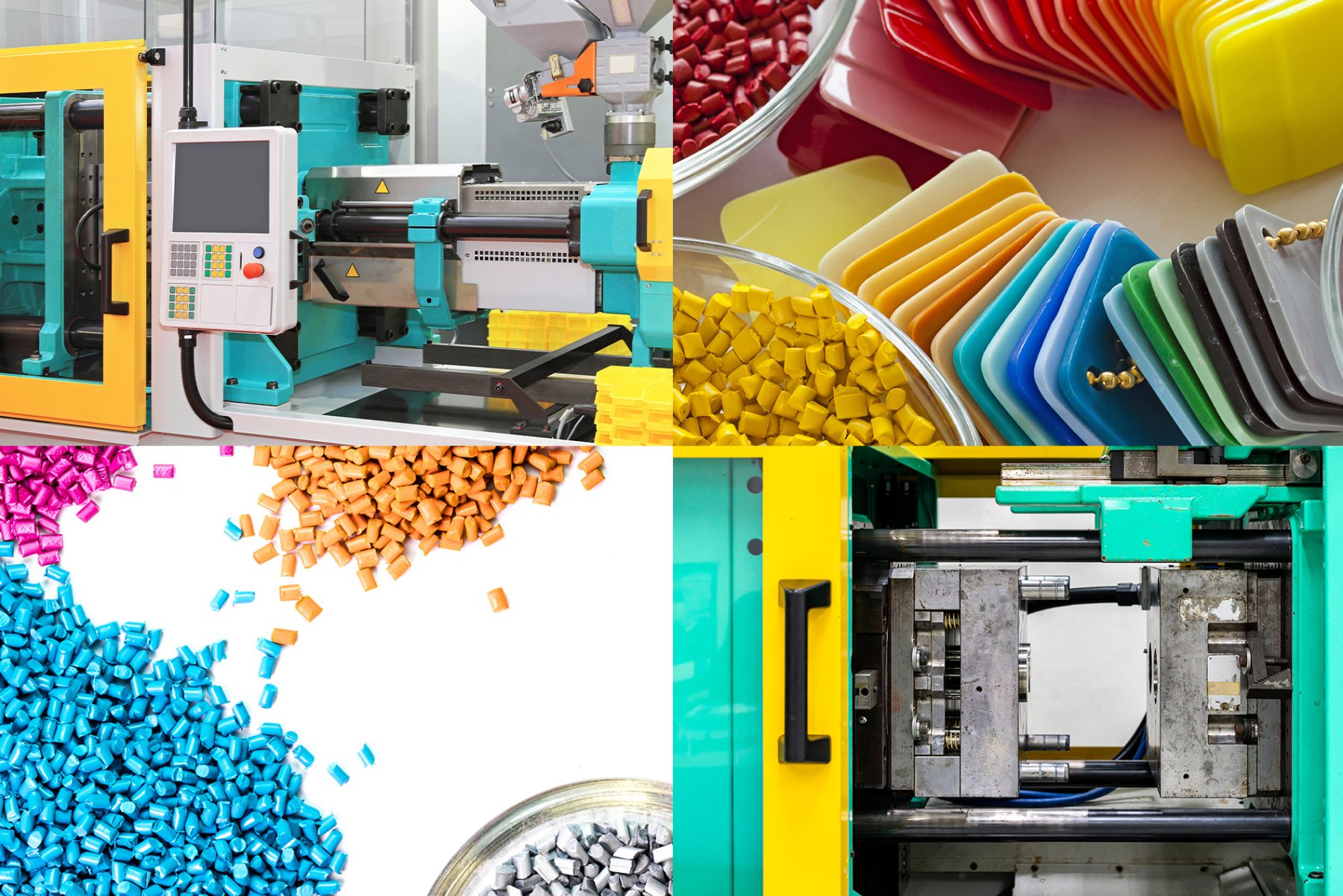
Rapid injection molding has become a game changer for several industries, streamlining the product development process and reducing time to market. In the automotive sector, manufacturers utilize this technology for producing complex components such as dashboards, panels, and housings. The ability to quickly iterate and modify designs allows for improved performance and alignment with consumer preferences, significantly impacting the overall quality and functionality of vehicles.
In the medical industry, rapid injection molding is essential for creating precise and bio-compatible parts that comply with stringent regulations. From surgical tools to housing for devices like pacemakers and insulin pumps, the speed and accuracy of this manufacturing process allow for rapid prototyping and testing. This leads to faster product development cycles, which is crucial in a field where innovation can directly affect patient outcomes.
The consumer electronics market also benefits from rapid injection molding . Companies are able to produce intricate designs for smartphone cases, laptop shells, and other accessories more efficiently. This manufacturing method not only shortens the lead time for new products but also allows brands to adapt swiftly to market trends and consumer demands. As a result, businesses can introduce cutting-edge products at a faster pace, enhancing their competitive edge.
Future Trends and Innovations
As industries continue to seek faster and more efficient manufacturing methods, rapid injection molding is expected to see significant advancements. One of the key trends is the integration of smart manufacturing technologies, such as Internet of Things (IoT) devices and artificial intelligence. These technologies will enable real-time monitoring and optimization of the molding process, leading to enhancements in quality control and production efficiency. Manufacturers will leverage data analytics to predict and mitigate potential issues, making rapid injection molding not only faster but also more reliable.
Another promising development is the increased use of sustainable materials in rapid injection molding. With growing awareness around environmental issues, companies are exploring bioplastics and recycled materials as viable options for production. This shift not only aids in reducing the carbon footprint of products but also meets consumer demand for environmentally friendly alternatives. Innovations in material science will play a crucial role in expanding the range of materials that can be utilized in rapid injection molding, enabling diverse applications across various sectors.
Lastly, the future of rapid injection molding may include advancements in 3D printing technologies that allow for more complex part designs and geometries. Hybrid manufacturing processes that combine traditional injection molding with additive manufacturing techniques can facilitate rapid prototyping and lower production costs. This integration will enable designers and engineers to create prototypes and end-use parts that were previously difficult or impossible to produce, thus significantly enhancing the versatility and capabilities of product development across industries.